The solution for simulation experts
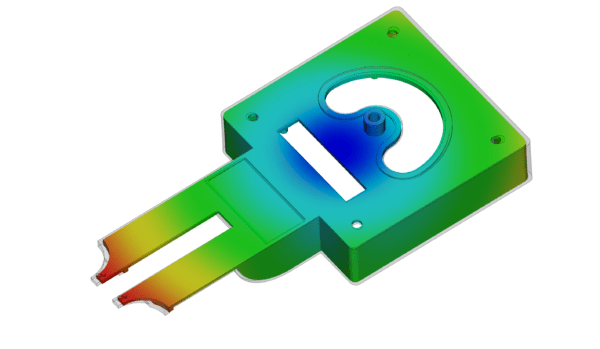
Detailed validation and optimization of part, tool and process
While small simulation solutions concentrate on the analysis of the part, Autodesk Moldflow Insight allows the accompanying simulation across the entire process chain.
We are talking about three simulation phases: Article design (S1), tool design and tool construction (S2) and production (S3). With Autodesk Moldflow Insight, you can validate and optimize parts, molds, and processes individually and exclude potential defects and their causes.
In the associated product trainings, we pass on our years of experience to you and show you how you can use Autodesk Moldflow Insight to optimize parts, molds and processes across all process chains.
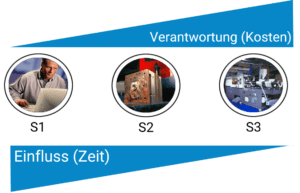
Simulation of complex parts, tool technologies and special processes
Parts:
- Fiber filled parts
- 2 component parts
- Insert and hybrid parts
- Metal or ceramic powder parts (‘green parts’)
- Duroplast and elastomer parts
Tool technologies:
- Tool inserts
- Conformal and variothermal cooling
- Cascade runners
- Modern hot runner technologies such as HRS FlexFlow
Special processes:
- Internal gas pressure processes
- Foam injection molding
- (Injection) imprinting
- Co and Bi injection molding („Sandwich“)
- and many more
High-grade parallelization through cloud computing
Extension of licenses. Increased computing power.
Insight customers can also run their simulations in the Autodesk cloud parallel to their own in-house computers. These are billed at flat rates. The cloud is particularly suitable for peak loads or complex calculations with a high number of elements, as it no longer blocks your own hardware and generates manageable costs in the cloud – regardless of whether the calculation takes 3 hours or 3 days. The Autodesk Cloud shows its full power in DoE calculations – parallel operation of up to 43 Insight licenses is possible with this solution.
Check out all new features within Autodesk Moldflow Insight 2025
Injection Molding Comparison Chart | Moldflow Adviser | Moldflow Insight | |||||
---|---|---|---|---|---|---|---|
Premium | Ultimate | Named User | Standard | Premium | Ultimate | Named User | |
Simultaneous local solving (max) | Unlimited | Unlimited | Unlimited | 1 | 3 | 3 | 3 |
Remote solving | - | - | - | ✔ | ✔ | ✔ | ✔ |
Cloud solving (using tokens) | - | - | - | ✔ | ✔ | ✔ | ✔ |
3D (tetrahedral elements) | ✔ | ✔ | ✔ | ✔ | ✔ | ✔ | ✔ |
Dual Domain | ✔ | ✔ | ✔ | ✔ | ✔ | ✔ | ✔ |
3D channel mesh (not supported on Linux) | - | - | - | ✔ | ✔ | ✔ | ✔ |
Midplane | - | - | - | ✔ | ✔ | ✔ | ✔ |
CAD solid models | ✔ | ✔ | ✔ | ✔ | ✔ | ✔ | ✔ |
Parts | ✔ | ✔ | ✔ | ✔ | ✔ | ✔ | ✔ |
Assemblies | - | - | ✔ | ✔ | ✔ | ✔ | ✔ |
Autodesk Helius PFA (Advanced Material Exchange) | - | - | - | ✔ | ✔ | ✔ | ✔ |
Autodesk Nastran | - | - | - | ✔ | ✔ | ✔ | ✔ |
ANSYS | - | - | - | ✔ | ✔ | ✔ | ✔ |
Abaqus | - | - | - | ✔ | ✔ | ✔ | ✔ |
LS-Dyna | - | - | - | ✔ | ✔ | ✔ | ✔ |
Code V (birefringence) | - | - | - | - | - | ✔ | ✔ |
Autodesk VRED | ✔ | ✔ | ✔ | ✔ | ✔ | ✔ | ✔ |
Elysium CADdoctor for Autodesk Moldflow | ✔ | ✔ | ✔ | ✔ | ✔ | ✔ | ✔ |
Command line API capable | - | - | - | ✔ | ✔ | ✔ | ✔ |
User interface API capable | - | - | - | ✔ | ✔ | ✔ | ✔ |
Solver API capable | - | - | - | ✔ | ✔ | ✔ | ✔ |